Table of Contents
In the dynamic manufacturing landscape, efficient asset management stands as a cornerstone for ensuring smooth operations and sustainable growth.
According to Deloitte’s 2024 Manufacturing Industry Outlook Report, the vast majority (83 percent) of modern manufacturers believe that smart factory solutions will transform the way products are made in five years.
However, many manufacturing units grapple with several challenges that hinder their productivity and profitability.
Let’s delve into five critical challenges faced by manufacturing units in asset management and explore how innovative solutions can effectively mitigate these challenges.
Addressing the Top 5 Asset Management Challenges in Manufacturing
1) Unplanned Downtime and Equipment Failures
Challenge: Unplanned downtime due to unexpected equipment failures can significantly disrupt production schedules, leading to delays and increased costs. This issue results in reduced production capacity, missed deadlines, and increased labor costs for emergency repairs, all of which negatively impact the overall efficiency and profitability of a business.
Ace Infoway’s approach to overcoming this challenge?Ace Infoway reduces unexpected equipment downtime using predictive analytics and real-time monitoring. We begin by setting up a specialized platform that analyzes historical equipment data from sensors. These sensors monitor critical equipment in real time, allowing us to track its performance continuously. Using advanced machine learning, we detect early signs of potential failures and send alerts for proactive maintenance. This approach includes customized preventive maintenance schedules based on our insights. Our solution aims to cut unplanned downtime by up to 30% and extend equipment lifespan by 20%. |
2) Inefficient Maintenance Practices
- Challenge: Relying solely on reactive maintenance instead of implementing preventive or predictive maintenance strategies can significantly impact operations by increasing failure rates and maintenance costs. This approach often results in higher repair costs due to the unplanned nature of fixes, more frequent and prolonged downtime that disrupts productivity, reduced asset lifespan as equipment wears out faster without regular upkeep, and elevated operational risks from unexpected breakdowns. By not proactively addressing potential issues, organizations face a cycle of inefficiency and increased expenses that could be mitigated through more forward-thinking maintenance practices.
“Research by McKinsey suggests that leveraging data analytics in predictive maintenance can result in a 30% reduction in maintenance costs.”
How can Ace Infoway tackle this challenge?Ace Infoway improves maintenance by using data computing services to solve reactive maintenance challenges. We create custom automated maintenance schedules using advanced algorithms and AI. This change from reactive to preventive or predictive maintenance reduces failure rates and maintenance costs by 25-30%. Businesses see a 10-15% increase in equipment availability, thanks to timely interventions and scheduled upkeep that minimize downtime and boost productivity. This approach also extends asset lifespan, lowers operational risks, and maintains efficiency and reliability across industries. |
3) Lack of Real-Time Asset Monitoring
- Challenge: Without real-time monitoring and data collection, accurately tracking the performance and condition of assets becomes challenging, leading to an inability to predict failures, suboptimal asset utilization, and difficulties in making informed decisions regarding maintenance and replacements.
Ace Infoway’s approach to overcoming this challenge?Ace Infoway uses IoT and real-time analytics to track how well assets perform. Sensors placed on assets collect data about their performance. This data goes to a central platform where advanced analytics quickly analyze it. This helps find patterns, potential issues, and ways to make operations better. Insights from this analysis predict when maintenance is needed, making operations smoother and helping manage assets better. This approach improves operational efficiency and asset use by about 20%. It also cuts inspection and audit times by 25%, ensuring assets are managed proactively and efficiently. |
4) Inadequate Inventory Management
- Challenge: Poor management of spare parts and inventory can result in significant operational challenges. Shortages can lead to production delays, halting manufacturing processes and affecting delivery schedules. Conversely, overstocking can incur high holding costs and risk potential obsolescence, further straining financial resources. Balancing these factors is crucial to maintaining efficient operations, and ensuring timely availability of parts while minimizing unnecessary inventory expenses.
How can Ace Infoway tackle this challenge?Ace Infoway tackles poor spare parts and inventory management by using advanced solutions. We analyze data to set optimal stock levels based on past use and future needs. This cuts holding costs by 15-25% and lowers stockouts by up to 30%, keeping production smooth and efficient. We also improve supplier relations and set up automated reordering for timely part availability, ensuring operations run smoothly and finances are maximized. |
5) Compliance and Regulatory Challenges
- Challenge: In manufacturing, asset management grapples with compliance challenges like safety, environmental standards, and operations regulations. Key concerns include maintaining accurate documentation, tracking maintenance, and ensuring data security. Compliance also covers supply chain management, environmental impacts, and mitigating risks from asset failures or regulatory shifts. Effective strategies integrate legal compliance, robust data management, and proactive risk mitigation for operational efficiency and regulatory adherence.
How can Ace Infoway solve this challenge?Ace Infoway improves manufacturing asset management by centralizing data, using predictive analytics to prevent failures, and ensuring robust data security to meet 95% compliance standards. We also optimize supply chain management to cut costs by 15%, improve efficiency, and provide ongoing regulatory advisory services, achieving 90% compliance. These efforts enhance accuracy in documentation, maintenance tracking, and risk management, thereby boosting operational efficiency and regulatory adherence. |
Addressing these pain areas typically involves implementing comprehensive asset management strategies, adopting advanced technologies like IoT and data analytics for real-time monitoring, and integrating maintenance management systems to streamline and automate processes. Ace Infoway’s Data Computing services can significantly mitigate the above challenges faced by manufacturing units in asset management.
Why Partnering With Ace Infoway?
- Deep expertise and experience: Our team comprises experienced professionals specializing in advanced data analytics, cloud solutions, AI/ML/Deep Learning, OEM product integration, and custom software development to build robust, scalable systems.
- Tailored solution only for you: We customize solutions to meet your specific business challenges, whether it’s a complex ERP, CRM, HRMS, SCM, Quality Management, Shop Floor system, a cloud-based platform, or a mobile app.
- Industry 4.0 Technology: We utilize cutting-edge tools and technologies to guarantee your software is up-to-date and future-proof.
- Quality and Efficiency: We prioritize quality through rigorous testing and assurance processes, ensuring efficient development for timely and cost-effective delivery.
- Collaborative Approach: We engage you throughout the development process, incorporating your feedback and insights to shape the final product.
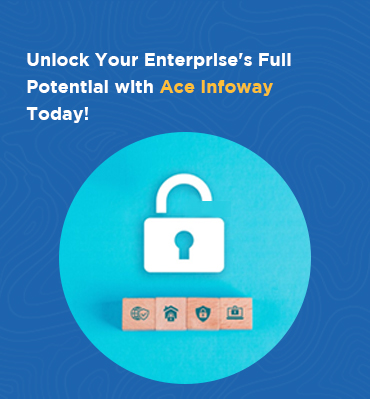
Conclusion
In manufacturing, efficient asset management using data computing can increase efficiency by 35%. It addresses challenges such as unplanned downtime, inefficient maintenance practices, lack of real-time monitoring, inadequate inventory management, and compliance issues through predictive analytics, IoT integration, and data-driven insights. By implementing these advanced technologies and strategies, businesses can optimize operations, reduce costs, improve asset utilization, and ensure compliance with industry standards, fostering sustainable growth and operational excellence.